Atlantic Poly Blog
Hand Held and Machine Stretch Film Protects Materials While Holding Them Together
At Atlantic Poly we offer a wide range of packaging film supplies. Our stretch film packing products include Extruded or cast Polyethylene Hand Held Film and Poly Stretch Film. It is available depending on your application. We also distribute stretch films and bundling films as cast or blown stretch films. Our films will improve your packaging cost. If you need a simple solution such as hand stretch wrap or, on a larger scale for pallet wrapping, we are the distributor for stretch films that companies use and trust.
Hand stretch wrap delivers superior puncture resistance and exceptional load retention. These properties make the hand stretch film the perfect choice for when you need a no frills stretch wrap. It is quiet, clear, and easy to release and rolls on smoothly.
Our Pallet Stretch Wrap is great quality and great value! It holds materials together safely while protecting them from dirt, moisture and theft. Top-quality polyethylene film offers outstanding tear resistance with superior stretch and cling.
Contact us today and let us fulfill your stretch film requirements with superior products and service.
Dumpster Liners Provide Additional Safety
Dumpster liners are a popular alternative to poly sheeting. They are also environmentally friendly; keeping hazardous materials contained therefore protecting workers, employees, and all others who may be in the immediate area. Made from polyethylene they provide a cleaner, safer, easier way to dump debris, and other airborne contaminants.
Atlantic Poly is a supplier of a variety of polyethylene dumpster and drum liners that help make waste disposal easier and safer. Dumpster liners reduce potential leakage, lower wash-out costs and increase container longevity. We carry products in standard stock sizes for quick delivery and can also customize our liners to meet your specific needs.
BinSkins are heavy-duty polyethylene liners, providing maximum protection for your roll-off containers. Liners from Atlantic Poly are rugged and tear-resistant and aid in the transport of solids and sludge liquids.
We have also developed a new line of Roll Off liners called “TRUE LINERS” which are guaranteed full gauge, full spec liners that meet all EPA and Government requirements. Current liners on the market are being sold at industry gauge tolerance +/- 10%. This has created numerous problems on various job sites where the EPA has actually refused dump trailers to be loaded because of under-gauge bags. Our “TRUE LINERS” are guaranteed and certified to meet full gauge requirements.
Bubble Wrap is Perfect for Shipping Fragile Items
Packing peanuts and bubble wrap are two popular packaging products used for protecting items when being shipped or stored. Which is best for providing packing protection?
When your business needs to pack or ship, obviously everything needs to be as secure as possible. However, for breakable items, an extra level of protection is required to maintain your business standards, reputation and efficiency. For this, there are a variety of packaging products available and one is bubble wrap.
Bubble bags are a fairly new innovation and very popular with all who are involved with the display, storage and delivery of fine artwork. They are also perfect for electrical components, glass, china and all things breakable.
While packing peanuts are good for filling the voids in boxes, when you are talking about wrapping fragile items, bubble wrap is best because it can be folded around the item for protection. It is unmoving and the item is perfectly protected and insulated.
Polyethylene Bubble Wrap provides outstanding protection from damage caused by shock, vibration or abrasion. Poly Bubble Wrap is easy to use and reduces packaging time and labor costs. Atlantic Poly is a Polyethylene Bubble Wrap supplier and Poly Bubble Wrap material comes in rolls, bags, sheets, dispenser packs or as anti-static.
Bubble bags with adhesive lips can be customized in a variety of sizes and weights. Contact us for sizes and prices on this high quality, transparent protection for fragile items.
Biodegradable Plastics from Atlantic Poly for Earth Day
Oxo-Biodegradable Plastic bags are better for the environment because the last up to 5 years indoors. But once they are exposed to UV rays or intense heat, they start to degrade into natural waste. The length of time it takes for oxo-biodegradable products to degrade can be ‘programmed’ at the time of manufacture and can be as little as a few months or as much as a few years.
There are different types of biodegradable plastic, and their costs and uses are very different. The two main types are oxo-biodegradable and hydro-biodegradable. In both cases degradation begins with a chemical process, followed by a biological process. Both types emit CO2 as they degrade, but hydro-biodegradable can also emit methane. Both types are compostable, but only oxo-biodegradable can be economically recycled.
The overall process, from polymer to water, carbon dioxide and biomass is called oxo-biodegradation.
How Does Oxo Biodegradable Plastic Work?
The plastic does not just fragment, but will be consumed by bacteria and fungi after the additive has reduced the molecular structure to a level which permits living micro-organisms access to the carbon and hydrogen. It is therefore “biodegradable.”
The chemical degradation process involves the reaction of very large polymer molecules of plastics, which contain only carbon and hydrogen, with oxygen in the air. This reaction occurs even without prodegradant additives but at a very slow rate. Pro-degrading additives is a catalyst for this reaction and increases the rate of the degradation. Degradation begins when the programmed service life is over (controlled by the additive formulation) and the product is no longer required. The rate of degredation is dependent on the formulation and the disposal environment.
There is little or no additional cost involved in products made with this technology, which can be made with the same machinery and workforce as conventional plastic products.
This chemical process has been well known to polymer scientists for years. The ability to manage these processes in a predictable way – to balance the effect of catalytic additives with the effect of contained antioxidants, allows the production of products that satisfy needs and can also biodegrade at acceptable rates.
Custom Made Poly Shrouds for Larger Items and Pallet Covers
For many companies, procuring the right packaging, can be daunting. This is especially true of polythene bags and shrouds. They come in all shapes and sizes, just about any thickness imaginable; some are welded at the bottom, some at the side. Some are printed in various colors; some have no print at all. For larger items many companies use pallet covers and pallet shrouds.
At Atlantic Poly Inc, these specialty custom made Polyethylene and Poly Plastic Shrouds can be made to fit most size objects and there is no minimum order. These polyethylene and poly shrouds can be manufactured from various types of film - low density, anti-static, mil spec material, etc.
There are different designs of low-density polyethylene (plastic) material to cover your palletized product with. There are differing manufacturing techniques, colors, prints, shrink capabilities, resins, and recycled. But if your company is a large quantity user of pallet covers, gusseted and seal on side or centerfold are very common. Both are made of polyethylene, come in several thicknesses and colors, and can be printed. To get a quote today on custom made poly bags and shrouds, contact Atlantic Poly Inc today.
Drum Liners Protect Employees and the Environment
In any industrial facility, the possibility of exposure to potentially hazardous chemicals or blood and body fluids cannot be ignored. And spills such as these pose health risks not only to employees, but can endanger the environment as well. Using drum liners would afford additional security against leaks and spills. DrumSkins™, Poly Plastic Drum Liners from Atlantic Poly Inc provide an extra level of safety, reliability and protection, especially when used for dense or viscous materials. Drum liners are a necessary precaution in keeping chemical contents separated from other materials and waste products.
Keeping up the level of safety and security in the workplace requires maintaining high standards of regulations and practices. And since chemicals such as oils, fuels and other materials which can all contribute to pollution, industrial facilities need to exercise extra precautions. Polyethylene Plastic Drum Liners are a step that would afford additional security against leaks and spills. There are many chemicals in the products and resulting wastes which are made and/or used in manufacturing. Many can prove quite dangerous to people's health and the immediate surroundings.
As a Polyethylene and Poly Drum Liner supplier, Atlantic Poly Inc provides a sensible, cost-effective and environmentally friendly method for storing, mixing and processing liquids, pastes and powders. Contact us for a quote.
Branding with Bags
Consider using custom plastic bags to promote your business. Using a branded bag to promote your business is effective when your business requires customers to use a bag to transport their purchases in. Having your company's logo on the bag, along with its name and tag line goes a long way in increasing the brand recall of your business.
Dry cleaners, grocery stores and deli’s are perfect examples of businesses that can use branded plastic bags from Atlantic Poly. Atlantic Poly’s Clear Dry Cleaning bags are made with hanger holes, sloped shoulders and are available in roll form for easy dispensing. Dry Cleaning Garment Bags on Rolls are perfect for protecting everything in your wardrobe from dust and dirt, and keeping them wrinkle free! We also supply both reusable and recyclable plastic grocery and shopping bags to many grocery store chains and retail stores across the US.
For branded plastic bags or printed poly bags with your logo or company information, we have the capabilities to imprint poly bags in up to eight colors on two sides. Keep in mind, the print needs to be bold and legible, and the message
should be easy to read from a distance. Generally, it is best to print
in a bold color with a font that is easy on the eyes. Printed Poly Bags, or branded plastic bags, are useful for many different industries. And, we can print as few as 5,000 bags. We also have complete layout and graphic services available for your convenience. For getting your name out there on bags, Call Atlantic Poly today.
Roll Off Dumpster Liners Decrease the Potential for Airborne Contamination
Many people will wonder, what is a Roll Off Dumpster Liner? A dumpster liner, in many ways, can be considered to be a massive garbage bag. However, many more attributes are used to specify dumpster liners, such as thicknesses, colors, sizes, chemical make-ups, uses, manufacturing techniques, and packaging. Even more importantly, there are many different liner requirements/types based on your company's specific application. Concrete companies, asbestos abatement companies, environmental service corporations, and others rely on Roll Off Dumpster Liners to contain materials which may be hazardous to public health or our environment. The liner is easily installed and the dumpster is ready to use in no time. in the US (varies by state), environmental laws require the use of dumpster liners. This is necessary so when a dumpster is being transported there is contaminated liquid dripping.
Many manufacturing facilities produce a daily amount of liquid refuse or semi-solid refuse. These companies use dumpster liners, or BinSkins for daily operation. BinSkins are mainly black opaque in color and thicknesses typically range from 3 MIL thick to 12 MIL thick. The most popular container sizes are 20, 30 and 40 yard. However, at Atlantic Poly we also make drum liners and liners are also made for larger applications such as railway trailers and truck trailers and you may request a quote for any of these larger sizes. BinSkins are easily installed by one person and are designed to have an overhang on each side, so that the liner may be secured by tying it off to hooks, and taping or tying in knots to avoid having it blow off. Contact Atlantic Poly for your BinSkins order.
Polyethylene Plastic and Disaster Preparation--Is Your Business Prepared?
Our hearts pour out to victims of natural disasters worldwide. Today, we focus on the immense suffering of the citizens of Japan. Sadly, the recent events in Japan serve as a stark reminder of the importance of business “disaster preparedness”. Obviously, for the Japanese business owners who took the wave head-on, no amount of disaster prep would have made a difference. However, just beyond the wave perimeter, unprepared business owners are “sunk” because they now lack the ability to protect investments from the elements.
Closer to home, this winter's massive snow crushed protective shelters all across America and exposed business plant, property, equipment, and inventory to the elements. Those owners who manage a proactive disaster preparation program maintain custom-made Poly Shrouds and Bags to blanket irreplaceable business machinery that don’t respond well to water.
We never get away from the threat of high winds, tornadoes, hurricanes, fire, and water. Somewhere today, a business owner in America will be victimized by the unexpected and will soon realize the immense value of his ready stock of Atlantic Poly Polyethylene Roll Stock sitting ready in the warehouse.
No business can afford to allow disaster prep to be an afterthought. Atlantic Poly stands ready to both prepare you for the unexpected and to help you sleep better at night for so doing.
Our Polyethylene Bags Have Many Purposes and Are Reusable
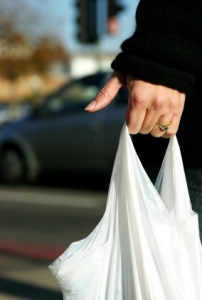
Plastic bags that need to be vacuum-free are made of more durable plastic and are closed from all sides except for a small opening through which the air is sucked out to create a vacuum inside before sealing it. Many of the bags Atlantic Poly provides are supplied to grocery chains, and when consumers use those bags they become useful bags for other items they own. Contact us today to learn more about our poly products and how you can get your supply of poly goods.